In recent years, the production and application of Active Pharmaceutical Ingredients (APIs) and Highly Active Pharmaceutical Ingredients (HAPIs) have met with growing interest. These highly concentrated active substances are used in drug manufacturing and can act on specific cells in the body, proving extremely effective even at very low doses. An increasing number of chemical and pharmaceutical products are being classified in these categories.
The Importance of Safety and Containment
Market demands are continuously growing, requiring increasingly advanced equipment, highly qualified personnel, and the implementation of rigorous procedures with targeted safety controls.
Equally relevant is the containment of these products. Due to their high concentration, APIs and HAPIs must be handled with extreme care to protect worker safety and minimize waste, considering their high value, both in economic and broader strategic terms.
When choosing a containment system, flexibility is an essential criterion: the ability to handle different products or adapt to future production needs represents a fundamental requirement.
The containment of APIs and HAPIs is, therefore, necessary to:
- Protect operators from exposure to highly active substances
- Avoid dispersion and waste of high-value products
- Ensure drug quality and safety
Classification and Exposure Management:
Occupational Exposure Limit (OEL) and Occupational Exposure Band (OEB)
For operator safety, OEL (Occupational Exposure Limit) thresholds have been defined, representing the maximum product concentration per cubic meter of air within which an operator can work for 8 hours without risks.
The OEB (Occupational Exposure Band) classes define the necessary containment level based on the active ingredient's hazardousness. OEL limits are typically managed in OEB classes, which define admissibility ranges:
- OEB 1: Open systems with local extraction (>1000 µg/m³)
- OEB 2: Downflow booth, valve containment systems (100-1000 µg/m³)
- OEB 3: Split valve, downflow booth, cone valve drum containment (10-100 µg/m³)
- OEB 4: Isolators, split valves, cone valve drum containment, continuous liners (1-10 µg/m³)
- OEB 5: Isolators, split valves with dedicated extraction/washing, drum containment (<1 µg/m³)
HAPI drugs generally require OEB 4 and OEB 5 because they are highly active and/or toxic principles, such as those for oncological therapies.
Italvacuum's High-Containment Solutions
To ensure maximum safety in handling APIs and HAPIs, Italvacuum has developed advanced containment systems for its CRIOX® System and Bi-EVOLUTION® industrial rotary dryers. These systems feature a closed and perfectly isolated interface, reducing the risk of environmental contamination during the loading and unloading phases. The design includes a fixed connection position and a mobile docking element that connects to the hopper securely and hermetically.
The containment system is based on an active valve and a passive valve, designed to ensure sealing of loading and unloading stations. The active valve, equipped with actuators, is installed on a steel structure or reinforced concrete leveling elements, ensuring operational stability and reliability. The passive valve is designed to operate in vacuum processes and is mounted directly on the rotary dryer, ensuring a safe and efficient workflow.
The CRIOX® System and Bi-EVOLUTION® dryers are also designed to optimize the production process, ensuring uniform drying thanks to their rotating bi-conical chamber, which allows homogeneous mixing and continuous mass revolution. Their vacuum operation makes them ideal for drying wet masses from centrifugation or filtration processes, ensuring maximum efficiency and final product quality.
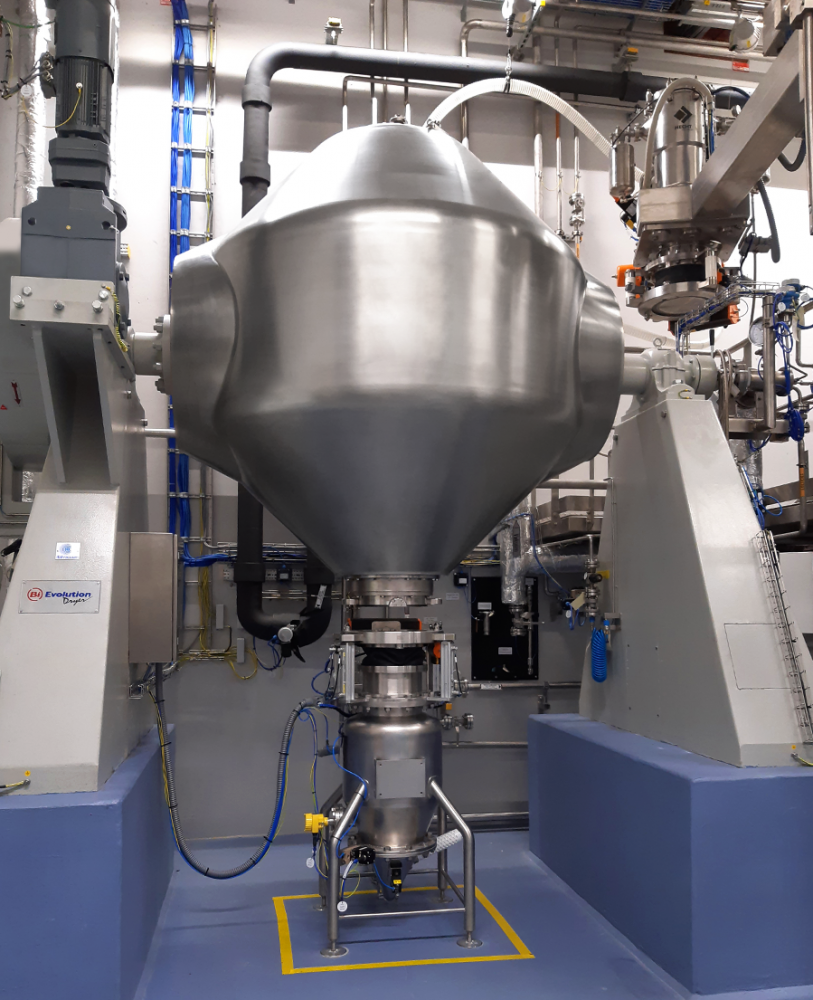
Active Valve and Passive Valve: Operation and Safety
The active valve forms the basis of the docking system. It consists of the seal housing, the seal itself, and the valve semi-disc. The two bayonet locking pins are installed in the active flange and serve to center the active valve with the passive one. All drives have limit switch micro-switches to detect their status and manage various operational sequences automatically. For docking and undocking, the active valve with its lifting unit is extended and retracted via pneumatic cylinders. The bellows are attached directly to the base plate and are extended or retracted following the stroke of the pneumatic cylinders.
The passive valve has no actuators or manual levers of its own and is mounted on the dryer. It also consists of the seal housing, seal, and a second semi-disc. After docking and locking, the two semi-valves are perfectly sealed against each other.
The coupling of the active valve semi-disc with the passive one allows, through the actuator mounted on the active part, simultaneous actuation, connecting the process apparatus upstream or downstream of the dryer itself, to execute the wet product loading and dry product unloading phases.
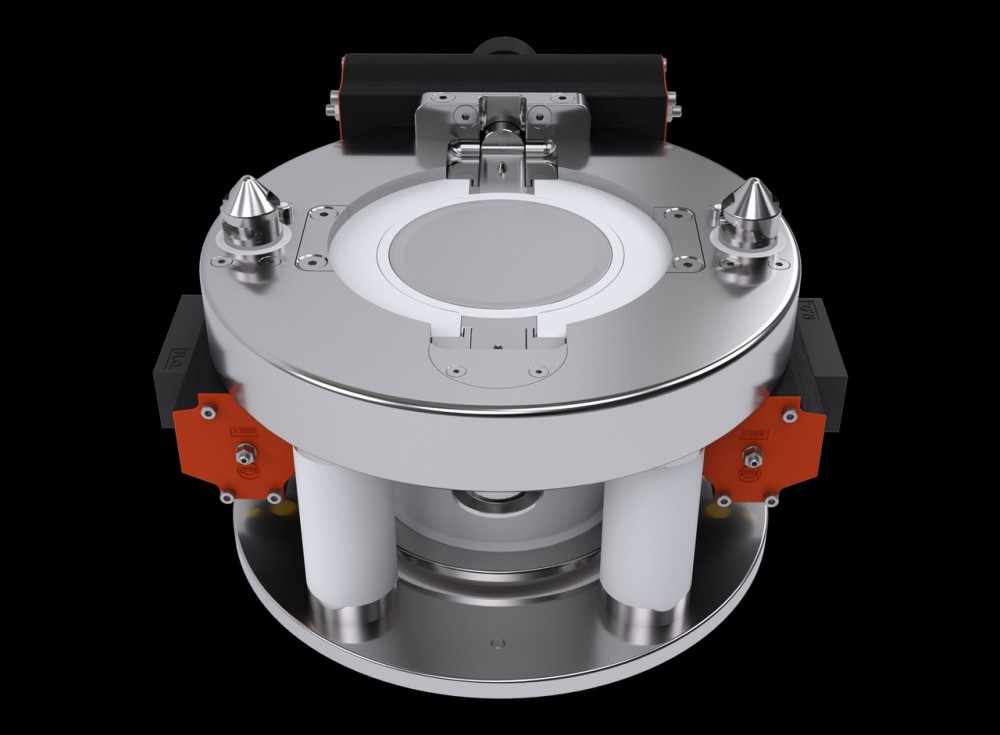
Performance and Safety Standards Compliance
This type of valve and coupling allows for OEL values <1μg/m³, effectively making the system compliant with OEB 4 and OEB 5 requirements. Measurement results depend on the application and product characteristics. Accurate and regular maintenance of the valves is necessary to achieve and maintain a high degree of containment.
Materials, Customization, Automation
These valves can be made in stainless steel or nickel alloys based on process requirements, and different non-metallic contact materials are available (EPDM, PTFE). PTFE is a chemically resistant non-elastic plastic material. The seal's durability strongly depends on product-caused abrasion.
The containment system is fully integrated into Italvacuum dryers' hardware and software control, enabling a safe and efficient automated process.
Conclusions
Italvacuum's equipment, the CRIOX® System and Bi-EVOLUTION® rotary dryers, are manufactured with maximum surface care, internally mirror-polished with roughness below Ra 0.4 μm to ensure minimum product accumulation and maximum vacuum tightness, combined with a high-containment system for product loading and unloading, thus allows for extremely versatile and effective equipment in vacuum drying processes, especially for high-value-added pharmaceutical APIs and HAPIs, utilizing proven and consolidated technology suitable for the most varied process conditions.
Andocksysteme, Italvacuum’s Partner for Reliability and Customized Solutions
Italvacuum has been collaborating with Andocksysteme, a world leader in high-performance containment systems for the pharmaceutical industry.
This strategic partnership integrates Split Butterfly Valves (SBV) and safe transfer systems for HPAPI powders into Italvacuum dryers, ensuring the maximum containment level (OEB 5) required for the safe handling of highly potent active ingredients.
Andocksysteme valves, recognized for reliability and precision in the pharmaceutical sector, ensure the safe transfer of active materials, perfectly complementing Italvacuum's vacuum drying technology.
This synergy offers customers complete and certified solutions for the safe handling of high-potency active ingredients.
Learn how the Andocksysteme Split Butterfly Valve for high containment powder transfer works in combination with the Italvacuum CRIOX® System and Bi-EVOLUTION® rotary vacuum dryers in this video: https://www.youtube.com/watch?v=Ieq8bajS1J8
For any information about our rotary dryers coupled with high-containment loading/unloading systems, please contact us at marketing@italvacuum.com